Frisky Pony
- Contractor: 1С-Rarus
- Automated workplaces (AWP): 10
- Implemented solutions: 1C:Drive
-
10automated workplaces, AWP
-
900labor costs, man-hrs
-
5client satisfaction, score
Groceries Online business process automation from scratch E-commerce processes.
- Execution period: November 2021 — June 2022
- Labor costs: 900 MAN-HRS
- Region: Germany
Functional areas
- Integration with Bitrix CMS
- Warehouse logistics
- Stockkeeper’s workplace
- Transport logistics
- Dispatcher’s workplace
- Mobile application for a driver
Industries
- Groceries Online
Description of the project
Groceries Online business process automation from scratch E-commerce processes have been fully automated by means of:
- Bitrix CMS — online store automation.
- 1С:Drive German Edition — automation of warehouse and transport logistics, and document management with end buyers.
- 1С Mobile Client — an application intended for drivers to get daily tasks and change order statuses.
Project history
Ajmalina GmbH is a company involved with innovation projects in Germany. Frisky Pony project is a startup involved in foodstuff delivery. You can oder products online or by phone; you can set a basic food basket that will be delivered at predetermined time slots. This project assists locals in coping with daily struggles during pandemic season. The desire to facilitate this process also involved us in automating all required business operations. For more details please see the description of the tasks and results of the project.
Project Tasks Completed
Integration with Bitrix CMS:
- export of product cards from 1C to the website;
- support for stock balances;
- import of orders paid by customers to 1C;
- export of vehicle availability data.
Warehouse logistics:
- bin warehouse management;
- zoning according to storage conditions.
Stockkeeper’s workplace:
- Improvement of order picking by storage locations.
- Product and box bar codes.
- Order packing by boxes according to size, weight and storage conditions.
- Interactive assistant when filling products — alerts for mismatched orders, dimensions, and storage conditions.
Transport logistics:
- Building routes on the map based on the orders.
- Possibility to specify the point of departure and final arrival of the driver.
- A mobile app for drivers designed to confirm order statuses and that the customers can interactively sign the delivery documents, if required.
Dispatcher’s workplace:
- Determination of vehicle quantity to deliver orders.
- Algorithm for calculating box positioning in vehicles depending on the zone and delivery time.
- Schedule of vehicle availability, when fully loaded, and reflection of the current data on the site.
Mobile application for the driver:
- list of orders and boxes for specific time slots;
- order delivery routes;
- order statuses: delivered/delivery failed.
Articles about the project
A customer places a non-repeat or repeat product order at Frisky Pony. The delivery service is possible not earlier than the next day. You can select a delivery slot and point according to the served region.
Orders are imported from the website to 1C:Drive every 10 minutes.
A manager confirms the availability of goods and sets a new order status «Awaiting order‑picking».
At the end of the shift (working‑day) the manager combines orders by delivery regions and slots and generates a Packing Slip document.
The storekeeper receives the Packing Slip document and sorts orders by order types (chilled or normal storage conditions). After that 1C:Drive calculates the required number of boxes by product size and weight and prospectively puts them in the boxes of a certain type and quantity. Then when you physically select a product and scan it, the system will check whether the storekeeper is trying to put the product in the right box.
The storekeeper sorts goods by their bin location in the warehouse. He/she comes to each bin and puts products in the required box with the bar code scanner.
The system verifies the quantity required by the order and free space in the box, and if the box is full, the system indicates this and suggests taking another box. If a storekeeper agrees with the system, this box becomes unavailable for filling. If there is more space left, the storekeeper continues filling the box and then manually makes it unavailable for filling. When there is no more room in the box or the order has been assembled, all boxes must become unavailable for filling, and there must be no more products left in the Order table.
After the order-picking is completed, the storekeeper closes the Packing slip and the system receives a confirmation on the quantity of boxes and calculates required space in the vehicle for their delivery. Now we can create a Transportation Order. This document shows how many vehicles will be required for the delivery of orders in the Zone within specified time slots.
After all Transportation orders have been generated, a dispatcher forwards them to the server to calculate their routes and receives a unique route for each vehicle for the most efficient order delivery.
In the mobile app all drivers can see their routes and a list of goods with delivery details (phone numbers and addresses).
At the set time, the drivers load the boxes into the vehicle and deliver goods to the customer. If the customer is in place and has accepted the Order, there is an opportunity to sign in the app or the driver just indicates that the order has been delivered.
If the client was not on spot, the driver assigns this order the ‘Delivery failed’ status. The return of the goods is documented with the Credit Note.
At each step, the system changes the order status that is also sent to the website, email or other way to notify the customer.
Key results of the project
- Storekeeper’s workplace for order picking.
- Adjustment of goods sorting in the warehouse by cell and storage type.
- Automated calculation of your need in boxes by storage types and vehicle space.
- Warnings of insufficient space or choosing the wrong box type when assembling goods.
- Routing according to customer requests for delivery slots.
Need a consultation?
Get in touch!
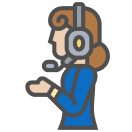